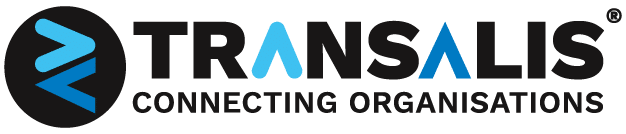
Since the pandemic, retail businesses have leaned towards localised micromanufacturing networks for the production of goods.
The widespread closure of international borders during this unstable economic period highlighted the fragility of international mass manufacturing operations. This is not least due to the distance away from the intended market, but also the reliance on singular large-scale manufacturers, as shown in the example below…
This blog forms one chapter of our published report: 3 steps to a shorter, greener supply chain. Download your free copy of the full whitepaper to discover innovative strategies for sustainable business.
Until January 2023, China remained closed to international visitors, when most other countries had already reopened their borders. The strict lockdown rules in China during this period have had significant knock-on effects commercially. One example in particular, which hit the headlines, was the lockdown of Foxconn’s mega manufacturing facility and its impact on the release of the iPhone 14. For tech giant Apple, this situation served as a costly lesson in their reliance on singular mass manufacturing operations outsourced to China. For the retail businesses that watched the situation unfold, it served as a catalyst to ensure economic resilience with more agile operations.
For the purpose of risk management, research by Forrester has shown organisations are now turning to localised manufacturing networks.* This is because switching away from large-scale international production to a networked manufacturing approach has significant associated benefits, such as supply chain optimisation. The same report also highlights that 58% of European consumers prefer more environmentally friendly products.
Therefore, organisations must consider the strategic advantages of local sourcing and manufacturing for retail businesses. Implementing a micromanufacturing strategy not only avoids future manufacturer mishaps (as experienced by Apple), but also means organisations can prioritise sustainability as part of their Corporate Social Responsibility (CSR). Therefore, with a local manufacturing strategy in place, organisations can shorten their supply chain, which results in greater sustainability credentials and an increased market share.
This blog explores the benefits of local-for-local manufacturing and the considerations for businesses embarking on this strategy.
In short, the benefits of switching to localised micromanufacturing for retailers are as follows:
Facilitates faster turnaround times and on-demand production
Enhances risk management of potential production issues
Shortens distance between the point of manufacture and the intended market
Provides scalability and flexibility for greater supply chain efficiency
Enables sustainable manufacturing practices for a reduced carbon footprint
Cuts transportation costs and complexities of international trade legislation
The commercial benefits of developing a more agile and shorter supply chain by implementing a micromanufacturing strategy are clear. But whilst the need for change is accepted, organisations may find implementing it in a timely and cost-effective way challenging.
The main challenge for retailers looking to switch to a localised manufacturer network is ensuring they can match supply and demand in an efficient way.
For this purpose, these organisations need to ensure that all the necessary data is visible. This includes sales reports, stock availability, production lead times, and market forecasts. Hence, the cost-effective management of a smaller-scale manufacturer network requires automation and integration. However, scaling the number of manufacturing suppliers and then integrating each one is a complex task. This is because it is highly likely that each new supplier will have different levels of competency to support the digital exchange of critical information.
Therefore, retail businesses looking at a micromanufacturing strategy should onboard automation technology to manage the data exchange process.
The business trend of using multiple localised micro-manufacturers is a necessity in minimising the threat of manufacturing delays. However, with an increased number of manufacturing suppliers, there is a risk that the complexity and cost will undermine the potential benefits of a broader supply chain.
However, harnessing a digital transformation layer allows organisations to overcome this complexity. The visual below demonstrates how it works:
As shown in the workflow, implementing a digital transformation layer removes the data format variations between supply chain connections, standardises it and feeds it to the correct endpoint automatically. So, whether the manufacturer uses scanned documents, CSV extracts, PDF files or EDI, this technology simplifies processing and ensures organisations can exchange accurate data.
The other critical factor is the speed of onboarding new connections. Research carried out by Transalis found that it takes an average of two months to onboard a local supplier. However, with a suitable onboarding plan in place, this timeframe can be drastically reduced. Transalis offers two viable options in onboarding management:
The first, as outlined in a recent case study, leverages the flexibility of APIs. Transalis worked with the client, who needed to onboard 15 platform integrations and over 300 suppliers within a 90-day window. For projects of this scale, it is imperative to have a clear onboarding strategy in place where all the necessary stakeholders are actively engaged. Transalis delivered on this objective, with the final solution pushed live after just 9 weeks. Since then, the client has entrusted Transalis to onboard an additional 100+ customers and has been named their provider of choice for all future digital transformation projects.
Another, equally effective option is a self-serve EDI model. Here, the manufacturer can set up their own connection via a white-label website powered by Transalis eDI Instant™. By automating the EDI configuration process, we have reduced the typical onboarding time in the industry from months to as little as 24 hours for most connections. This ensures all of your manufacturers are connected in the same way and can consistently communicate accurate digitised information with you 24/7.
At Transalis, we have a tried and tested rapid onboarding strategy that encompasses all the necessary stages to run as smoothly as possible. As detailed below:
Stage 1. Recruitment: Identify the delivery team across all parties and define their roles/responsibilities
Stage 2. Engagement: Outline the plan to all parties to confirm the project scope, identify potential roadblocks, and set timelines
Stage 3. Enablement: Start onboarding following project sign-off, with multiple, simultaneous work streams
Stage 4. Handover: Transition from production/operational teams to support and CX for ongoing management
Switching from a small selection of larger-scale manufacturers to a higher volume of smaller-scale manufacturers has the potential risk of increasing operational costs. As outlined in the previous sections, managing a small batch production network can be complex, as the required flow of data between all the relevant parties is vast, involving various formats and endpoints. It is therefore imperative that the technology that is onboarded to manage this complexity and scale is kept within a reasonable budget to allow for the cost-effective production of goods.
An integrated digital transformation solution supports scalable and agile operations, whilst also minimising the cost of onboarding new business technologies. As highlighted, utilising supply chain technology that standardises and feeds the data that’s received from multiple sources means it can be managed under a single SaaS solution. This approach is preferable, instead of managing multiple individual supply chain connections – an approach which can drastically increase the cost. For this type of technology requirement, we would advocate for a singular-layer integrated solution, as it can easily facilitate a micromanufacturing network for retail scalability and flexibility.
If you’d like to discuss how automation and integrations solutions can support an efficient and agile micromanufacturing strategy then get in touch via 0845 123 3746 (UK callers) or +44 1978 369 343 (international callers), or email sales@transalis.com. You can also find an abundance of additional resources in our Knowledge Hub, including; educational blogs, topical whitepapers, and client case studies.
*Forrester. 2022. European Predictions 2023: Highlights.